Innovative Efficient Design
Because of its innovative, highly efficient design, SPAH utilizes at least 20% less land than a conventional plant with similar output capacity. This means your organization will save at least 20% upfront in land and environmental costs.
With its smaller footprint, SPAH also provides significant savings in capital, operational, maintenance and entire life cycle costs, making it the green facility solution of the future.
Modular Design and Construction
The standardized template SPAH and its modular approach, greatly streamlines planning, and saves valuable time in the concept, design, qualification and construction stages of the project.
SPAH modules are pre-constructed, with all equipment installed, tested and validated in a controlled environment, enabling quick and cost effective changes prior to shipment. This ensures quality and predictability in the construction process, and shortens delivery time.
With SPAH modules, your complex and state-of-the-art production facility can be up and running, anywhere in the world, in less than 18 months… allowing your products to be launched faster, and sales and cash flow to be realized sooner than ever possible before!
Modular Production Flexibility
With SPAH’s modular construction, you can quickly and easily modify production assets to meet ever-changing business requirements.
Maximize profits by increasing a product line’s capacity to meet surging demand for a blockbuster…or reduce capacity to cost-effectively produce an established product. Worried about the impact of a drug launch failure? With SPAH, you simply retrofit the production line!
This modular flexibility not only mitigates business risk, it provides a strategic advantage to roll out more products in a faster time.
Pre-Fabricated “Plug and Play” Modules
SPAH modules are pre-constructed, with all equipment installed, tested and validated in a controlled environment, enabling quick and cost effective changes prior to shipment. This ensures quality and predictability in the construction process, and shortens delivery time.
SPAH production modules feature patented “plug and play” technology and can be easily changed without disrupting other production lines. And, changes take only days, not weeks or months like in a typical conventional plant, maintaining continual sales and cash flow.
SPAH’s modular flexibility ensures it will always be a highly efficient, cost-effective production asset, immune to obsolescence.
Embedded Pilot Plant
SPAH features an embedded pilot plant, integrated in the production facility. This provides immediate cost savings in land and capital by not having to build and maintain a separate pilot plant facility.
Developing clinical batches in the same building as commercial scale makes reproducibility and repeatability much easier. And, quality issues, such as those associated with different air and water sources, are completely eliminated.
With the added convenience of having the development team and scientists in the same building as production, technology scale-up, transfer and commercialization are faster, consistent, and more economical than ever before!
This quality and regulatory friendly environment can greatly reduce approval times, and give your organization a significant competitive advantage with faster and more frequent quality drug launches.
Glass Viewing Gallery
SPAH’s innovative hub-corridor design features a unique, highly impressive glass-viewing gallery overlooking the entire production area.
Everyone enjoys a factory tour, and this powerful feature can be leveraged as a convenient and cost effective marketing tool for both sales and public relations. And now, all this can be done without the need to gown-up!
Automated QC/QA with SPAH Hub Box
SPAH’s hub-corridor design makes it easy to comply with future FDA, regulatory, or internal requirements for automated QC/QA systems such Process Analysis Technology, or PAT. With automated QC/QA capability, production batches are monitored, quality tested, and released using real time data.
SPAH’s patented “Hub Box” technology interfaces with the production modules to provide instant “plug and play” process validation and quality control. With instantaneous testing of any batch, compared to the “several days” required for a traditional batch testing approach, you will enjoy faster batch release to market time and faster revenue.
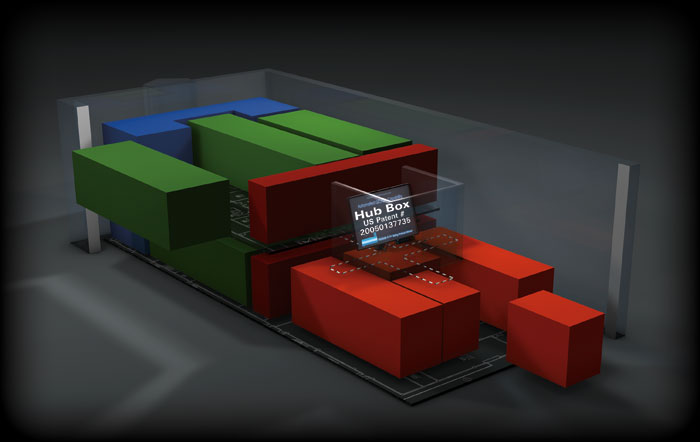
Example of SPAH’s superior output per total facility area footprint
(due to innovative reverse engineering of overall facility space).
Target Production
|
200-300 million tablets per year
|
Average Tablet Weight
|
500 mg
|
Total Processing Weight
|
150 Tones per year
|
Batch Size
|
250 Kg
|
3 Batches / Day
|
180 Tones (given 240 working days per year)
|
Process
|
IBC Systems with direct compression, coating, blister packing with provision for fluid bed, microwave granulation drying. Processing and operational equipments are predominately European technology.
|
Compliance and Automation
|
Current and future FDA requirements for Process Analytical Technology (PAT) due to the Hub-Process configuration.
|
Footprint
|
About 75m by 45 m, 2 floors, with manufacturing suites floor area of 3600 m2. Pilot production suites about 300 m2.
|
Total Project Cost (in Singapore)
|
S$39M (vs. typical S$45M or more)
|
Ability to Execute Project
|
Worldwide, prefer operation (contract production) to be in Singapore - but not ruling out other locations.
|
Global Engineering Foster Wheeler’s and our SPAH One design basis. These comparison numbers are highlighted in Table A, Page 4 of ISPE article available for download at: http://www.spah.info/docs/06JF_Brocklebank.pdf